Today we discuss electro-spark deposition's apply in metal alloys , at the same time we will focus on this technology how to modify the mold in injection molding tooling and casting molds.
What is Electro-Spark Deposition?
Electro-spark treatment, also known as Electro-discharge machining (EDM), is a specialized manufacturing process that involves the use of electrical discharges to shape and modify the surface of metal parts.
During Electro-spark treatment, an electrical discharge is generated between an electrode and the workpiece, typically made of conductive materials such as steel or alloys. The process begins by placing the electrode, often in the form of a small, shaped tool, in close proximity to the workpiece.
When a voltage is applied between the electrode and the workpiece, a series of rapid electrical discharges occur. These discharges create intense heat, melting small portions of the workpiece's surface. The molten metal is then quickly quenched by the dielectric fluid, causing it to solidify and form tiny craters or indentations.
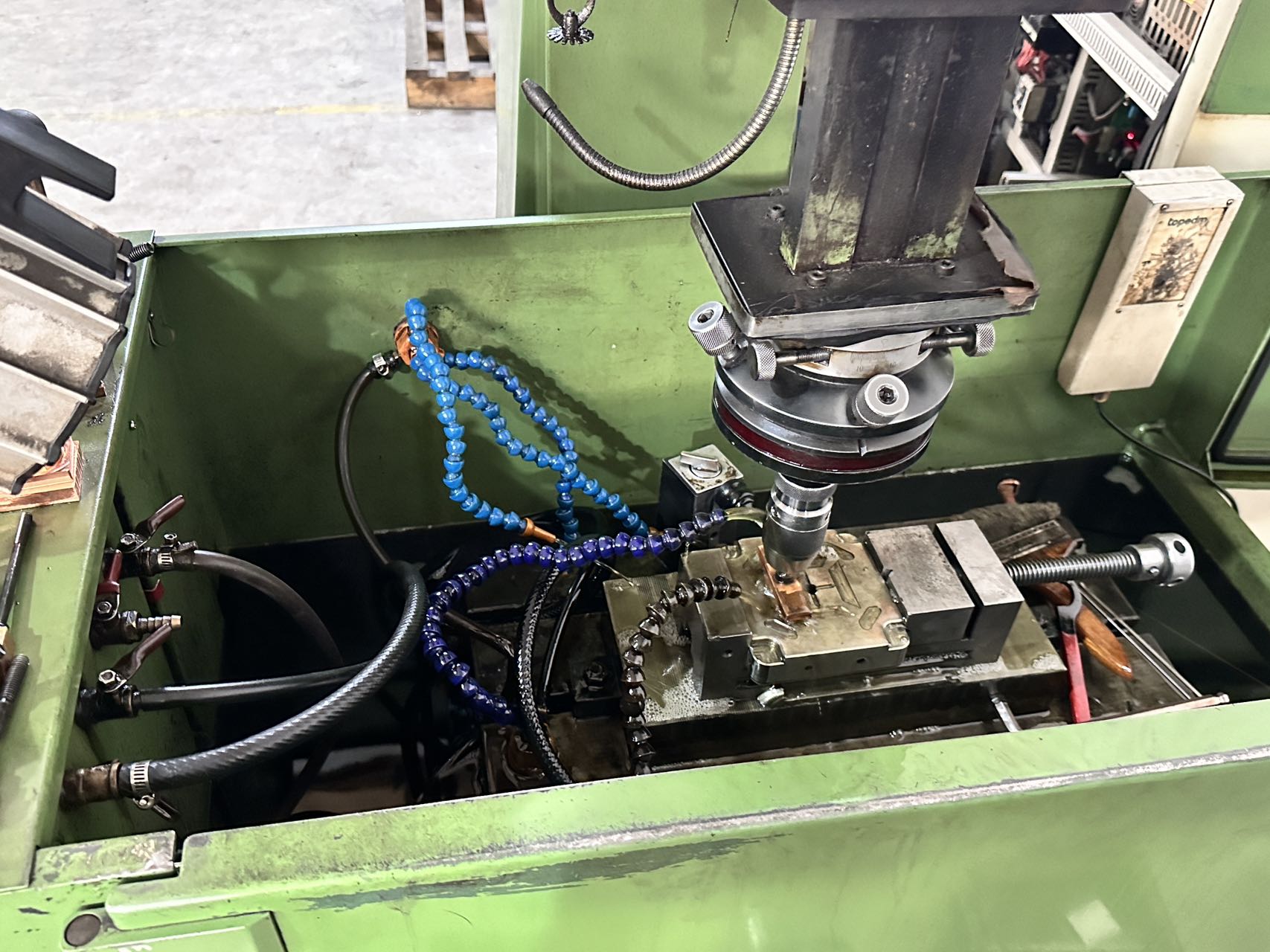
ESD applied to metal alloys
When the capacitor energy is released, the direct current creates a high-temperature plasma arc between the electrode tip and the metal alloy workpiece. This high temperature range is between 8000 and 25000°C. The plasma arc ionizes the anode and quickly transfers the molten material to the workpiece.
This ionizing anode is transferred to the substrate via short pulses. The high-temperature arc consists of anode particles, a heat stream (hot jet), and a plasma created by the decomposition of gases and reactive atoms of nitrogen, oxygen, and carbon. Most of the heat is carried by thermal jets and plasma.
Because the pulses are short, heat transfer through the thermal jet and other gases is minimal, and the only heat transfer to the substrate is through the small number of anode particles deposited on the substrate. Therefore, these pulses transfer a small amount of heat to the substrate without changing the microstructure of the substrate. This method is more advantageous than the fusion welding process typically used to repair alloys with poor heat-affected zone properties (e.g., low toughness, high hardness, liquefaction cracking).
Additionally, the process helps create a strong metallurgical bond between the substrate and coating. Microalloying between the electrode melt and the substrate initiates the formation of plasma through air decomposition, carbonates, carbides and nitrides.
Advantages
1.Precision and Accuracy: Electro-spark treatment allows for precise and accurate shaping of intricate details and complex contours on metal surfaces. The controlled electrical discharges erode the material in a controlled manner, enabling the creation of precise features such as small holes, slots, or indentations with high dimensional accuracy.
2.Preservation of Material Integrity: One of the significant advantages of Electro-spark treatment is its ability to preserve the hardness and integrity of the workpiece. Unlike traditional machining methods that can generate excessive heat and induce unwanted changes in the material properties, Electro-spark treatment minimizes heat-affected zones and maintains the workpiece's hardness and structural integrity.
3.Complex Geometries: Electro-spark treatment enables the machining of complex geometries that may be challenging or impossible to achieve with conventional machining methods. Its ability to shape intricate features allows for the production of molds, dies, or other components with unique contours and intricate details, expanding the design possibilities.
4.No Tool Wear: Unlike traditional machining methods that involve cutting or abrasion, Electro-spark treatment does not involve direct contact between the tool and the workpiece. As a result, there is minimal tool wear, leading to extended tool life and reduced maintenance costs.
Summary
This article mainly introduces the EDM process in the mold making process, not only introducing its process flow, but also introducing the main advantages of this process. Through the above video, I hope you can understand the process more clearly. If you have other questions, please feel free to contact us.
Post time: Jun-07-2024